Scratch Builders Goes Out on a Limb
July 21, 2025
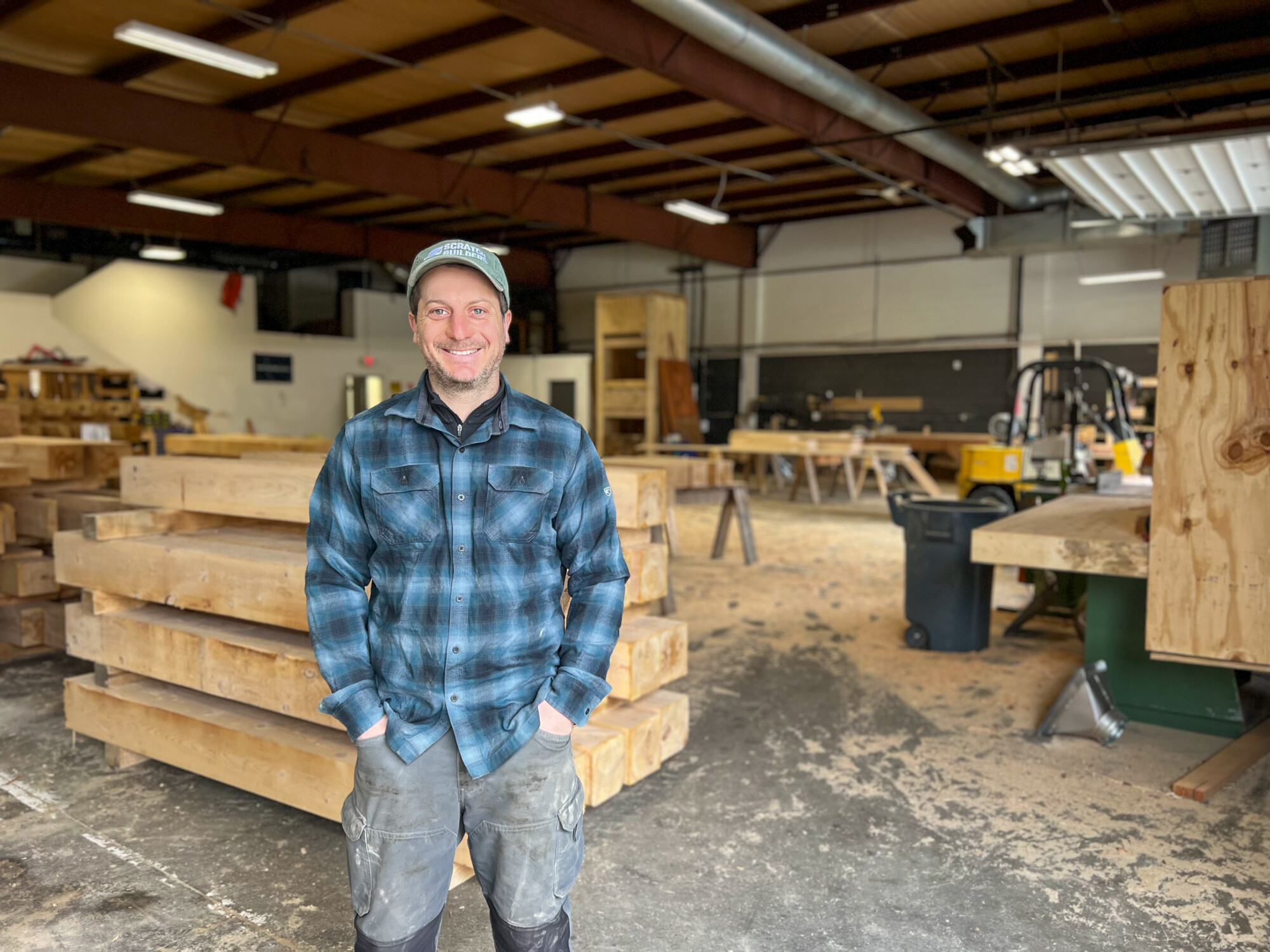
An early adopter among Vermont builders, the company is advocating for mass timber.
By Christine McGowan, Vermont Sustainable Jobs Fund
Evan Taubes, owner of Scratch Builders in Williston, Vt., is among a few builders working to advance the mass timber industry in Vermont. “If no one is presenting it as an option to clients, then the choice will continue to be timber framing or steel,” said Taubes. “We’re sticking our neck out a little when we see an opportunity that would be a good fit for mass timber because it aligns really well with our values.”
High among those values is building with sustainable materials. “It’s about caring for the environment, high-quality buildings, and beauty in spaces,” he said.
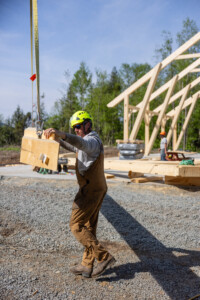
Courtesy of Scratch Builders. Photo by Stina Booth.
Drawn to the craftsmanship and natural beauty of timber frame structures, Taubes opened Scratch Builders in 2015 building primarily timber frame homes and barns. Mass timber, he says, sort of showed up on his doorstep. “Our core mission has always been to work with sustainable products, specifically wood,” he said. “It’s a great fit for us because we’re already good at working with heavy timber,” he said. “There are a lot of hurdles to mass timber at this early stage, but I really believe in it. I like what it can achieve.”
The biggest hurdle, according to Taubes, is that few of his clients have ever heard of mass timber. “It’s challenging to sell a product that nobody knows about,” he said. “But, if we didn’t talk about it, then how would anyone ever choose it? They call us because they want a timber frame. If the project lends itself better to mass timber and I try to suggest that, they’re like, what’s mass timber?”
So, what is mass timber?
Mass timber is an umbrella term that refers to a variety of engineered wood products composed of multiple solid wood pieces that are nailed or glued together. Considered a low-carbon alternative to concrete and steel, mass timber was recently utilized in a highly publicized expansion at the Fairbanks Museum & Planetarium. It’s also slated to be used for an upcoming project at the Patrick Leahy Burlington International Airport.
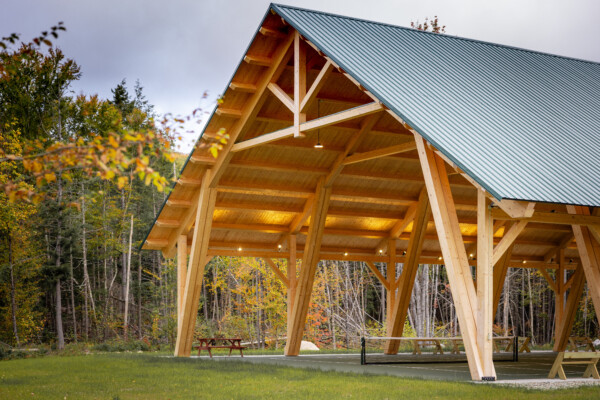
Photo courtesy of Scratch Builders.
The engineered wood products are gaining momentum as the building industry looks to reduce its carbon footprint. Currently, the built environment is responsible for about 42 percent of annual global carbon emissions, largely due to the carbon-intensive process of extracting and manufacturing cement, iron, steel, and aluminum. Although wood has long been acknowledged as a renewable alternative, cutting trees that are suitable for framing large structures poses its own quandary. “Those really big, really long trees are one in a million,” said Taubes. “We don’t want to cut those down and, even if we did, you can’t build an industry around that.”
Mass timber, on the other hand, is manufactured from smaller diameter trees often considered “low-value” in the forest. The smaller pieces are layered and glued or nailed together to create strong, structural load-bearing beams and panels. “We no longer need big trees for big beams,” said Taubes. “We can achieve the same aesthetic and sustainability goals using mass timber.”
Proof of concept
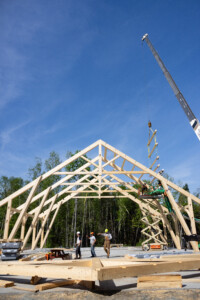
Courtesy of Scratch Builders. Photo by Stina Booth.
Scratch recently completed a mass timber pavilion for Copper Cannon Camp in Bethlehem, New Hampshire. The camp wanted to cover a large sport pavilion encompassing a full size basketball court and a couple of pickleball courts–about 6,000 square feet in total. “They were getting estimates for a steel, hoop style building,” said Taubes. “It was expensive, ugly, and not a permanent structure. At best they would get twenty or thirty years out of it.” They asked Taubes if he had another solution.
“It was an ideal use case for mass timber, “ he said. “It’s simpler and less expensive than traditional timber framing for a space that size, it’s beautiful to look at, and it has a much longer life cycle–a hundred years at least–so it’s a better value.”
The project uses European spruce glulam beams and eastern spruce from White Mountain Lumber, which Taubes milled in his wood shop, for the roof decking. Mass timber is currently not manufactured in New England, although many in the industry are hopeful that will change in the coming years.
“Even with the glulam beams coming from Europe, the carbon footprint is better than steel,” said Taubes. “They come by boat and the factories in Europe are all close to the ports. This project was unique in that we were able to also use locally-sourced wood for the decking.”
Scratch Builders is in the pre-construction phase of a second mass timber project in Vermont, this one residential. “In this case, the client knew exactly what they wanted,” said Taubes, “a cross-laminated timber house with very few beams. It’s pretty much all mass timber panels, which are strong enough to eliminate the need for framing. So, they will get this very European, Danish modern look with a flat, spruce wall.”
While the cost-benefit of mass timber is widely seen to hit a sweet spot with larger, taller buildings, Taubes is looking forward to working with the homeowner, an architect, in a residential application. “It’s a very different project from the pavilion, driven in large part by aesthetics, and will really showcase what the panels can do.”
Investing in potential
While Taubes is quick to point out that his experience with timber framing lends itself well to working with mass timber, he acknowledges that there has been a steep learning curve. He considers it an investment in his business and a bet on the future of mass timber.
His company purchased a new CAD, or computer-aided design, program that was both expensive and challenging to learn, but necessary for coordinating complex shop drawings with mass timber suppliers. “That was the first investment,” said Taubes, “just so that we could interface with suppliers.”
Then there’s the time and resources he invests in educating clients about mass timber, explaining the benefits and creating detailed cost estimates for projects that may or may not come to fruition. “You really have to go out on a limb if you see a building that could be a good fit. But it’s worth it because if we can become strong at it and get proof of concept through a couple of projects, then we can help to lead the adoption of mass timber in Vermont.”
Taubes’ dream scenario is that locally-sourced eastern hemlock or white pine will be manufactured into mass timber regionally in the next ten to 30 years. That’s a dream, he says, that a lot of people share and are working to make a reality.
“Imagine if the world was just a little nicer,” he said. “Just a little better built, prettier to look at, with less impact on the environment. It’s possible, but if we don’t do the work of building the buildings, no one will ever see the product’s potential.”
About the Vermont Forest Products Program
Vermont’s forest economy contributes more than $2 billion in direct economic output and provides more than 13,000 jobs in forestry, logging, processing, specialty woodworking, construction, wood heating, maple production, and forest-based recreation. The Forest Products Development Program at the Vermont Sustainable Jobs Fund (VSJF) creates space for strong relationships and collaboration throughout the industry and promotes the development of new and existing markets for Vermont wood products. Learn more at www.vsjf.org.
Read More Stories Like This:
- The Forest Business Accelerator Seeks Entrepreneurs for 2025 Cohort
- Reimagining a forest products industry that solves problems for people and planet
- Business Sense – FREE training series for entrepreneurs and small business owners
- Rockledge Farm Woodworks: A Father-Son Furniture Making Business Navigates Growth, Transition
- Sawyer Made Balances Growth with Tradition
- WheelPad Entrepreneur Julie Lineberger is Keeping Families Together